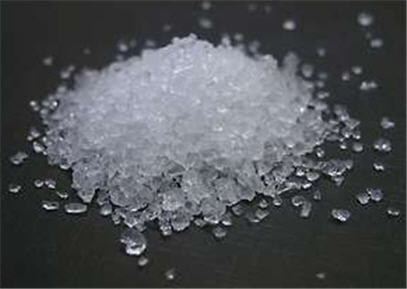
The very short, quick answer to the question, “Does drywall contain silica?” is yes. If you were simply looking for a one-word, yay or nay answer, well there you have it. If you’d like more details that expand on the answer, then please read on.
Background
There are several issues at play here. At the very core of the issue is the fact that exposure to airborne silica and silica dust can cause serious health issues. The Occupational Safety and Health Administration, OSHA, has issued new rules regarding exposure to silica in the working environment. This new rule set went into effect as of September 23, 2017.
In OSHA’s overview of the health hazards posed by silica inhalation, four critical conditions are given attention: Silicosis, Lung Cancer, Chronic Obstructive Pulmonary Disease (COPD), and Kidney Disease. Here is what OSHA says about each:
quoted from OSHA’s statement on Health Effects, Silica, Crystalline which can be found here.
Silicosis
Breathing crystalline silica dust can cause silicosis, which in severe cases can be disabling, or even fatal. When silica dust enters the lungs, it causes the formation of scar tissue, which makes it difficult for the lungs to take in oxygen. There is no cure for silicosis.
Silicosis typically occurs after 15–20 years of occupational exposure to respirable crystalline silica. Symptoms may or may not be obvious; therefore, workers need to have a chest x-ray to determine if there is lung damage. As the disease progresses, the worker may experience shortness of breath upon exercising. In the later stages, the worker may experience fatigue, extreme shortness of breath, chest pain, or respiratory failure.
Because silicosis affects the immune system, exposure to silica increases the risk of lung infections, such as tuberculosis. In addition, smoking causes lung damage and adds to the damage caused by breathing silica dust.
In rare instances, individuals exposed to very high concentrations of respirable crystalline silica can develop typical silicosis symptoms as well as fever and weight loss within weeks instead of years. In these cases, medical evaluation should be performed as soon as possible.
Lung Cancer
Exposure to respirable crystalline silica increases the risk of developing lung cancer. Lung cancer is a disease where abnormal cells grow uncontrollably into tumors, interfering with lung function. The abnormal cancer cells can also travel (“metastasize”) and cause damage to other parts of the body. Most cases are not curable.
Chronic Obstructive Pulmonary Disease (COPD)
Exposure to respirable crystalline silica increases the risk of other lung diseases, primarily COPD, which includes emphysema and chronic bronchitis. The main symptom of COPD is shortness of breath due to difficulty breathing air into the lungs. COPD is not usually reversible and may worsen over time.
Kidney Disease
Studies of workers exposed to respirable crystalline silica have found that these workers are at increased risk of developing kidney disease. For instance, kidney failure has been observed among workers with high silica exposure, such as in abrasive blasters who also were suffering from silicosis.
With specifics regards to silica in drywall, the Safety Data Sheet (SDS) issued by Georgia-Pacific pertaining to their brand of gypsum board (also called drywall) clearly states:
Gypsum (calcium sulfate) contains naturally occurring crystalline silica (quartz) which is listed as a lung carcinogen. See Section 8 for exposure information.
quoted from Safety Data Sheet linked above
The Safety Data Sheet provided by U.S. Gypsum pertaining to their gypsum board panels states:
The amount of respirable crystalline silica is less than 0.1%. The gypsum used to manufacture these panels contains respirable crystalline silica varying by source and over time, as determined by testing the gypsum bulk samples. Based on this data, the total respirable silica content of the panels may exceed 0.10 percent by weight.
quoted from page 1 of the USG gypsum panel SDS
Continental Products, in a company statement issued in response to the new OSHA silica regulations that went into effect on September 23, 2017, stated:
Recent guidance documents issued by the federal government and industry stakeholders refer to silica-free joint compounds. However, testing of both our products and our competitors’ products indicates that silica-free joint compounds do not exist from any manufacturer. Low concentrations of crystalline silica are present as a natural impurity in all limestone- and gypsum-based wallboard and joint compound products.
Statement by Continental Building Products, October 2017. The full statement can be found here.
The evidence is undisputable, crystalline silica is present in both gypsum board as well as joint compounds for finishing gypsum board (drywall). This CDC.gov page describes airborne silica dust when sanding drywall. The Safety Data Sheets provided by the manufacturers specifically address the amount of silica present in the products they produce. We could end our analysis here, having presented clear evidence of silica in drywall, however, there is one more relatively recent development that is very pertinent. There was a patent issued in 2013 regarding the manufacture of gypsum board. The abstract from the patent states:
Quoted from U.S. patent #WO2015069609A1
A gypsum composition, board, and method of producing a gypsum board with increased fire endurance are described. The set gypsum-containing composition can be used to prepare a gypsum board having fire endurance, based on the inclusion of silica gel.
Did you catch that? “based on the inclusion of silica gel.” So not only is silica naturally occurring and virtually impossible to eliminate from the manufacturing process of gypsum board, a patent issued in 2013 describes a process of adding silica (in the form of silica gel, we will get to that shortly) to increase the fire rating of gypsum board.
To provide some context in order to give you an understanding of what is the need for this invention, we will again look at the patent:
BACKGROUND OF THE INVENTION
[0001] Gypsum products can be generally manufactured using a slurry formed from at least water and stucco. The stucco, which is calcium sulfate hemihydrate (CaS04*½H20), reacts with water to form gypsum, which is calcium sulfate dihydrate (CaS04*2H20).
Gypsum wallboard can be a composite board comprising a core, face sheet, and back sheet. The density of gypsum wallboard can be reduced by adding aqueous foam to the stucco slurry in an amount effective to provide the desired gypsum core density. As the board contains less gypsum per unit volume, there is less crystallized water available to extend fire endurance of the wallboard. Gypsum wallboards are commonly used in drywall construction of interior walls and ceilings, and should be able to withstand both fire and excessive temperatures. As a result, gypsum wallboards are manufactured using specifications that maximize fire endurance/resistance.
Quoted from U.S. patent #WO2015069609A1
The above quote states, “The density of gypsum wallboard can be reduced by adding aqueous foam to the stucco slurry in an amount effective to provide the desired gypsum core density.” The question that the patent doesn’t answer as it relates to this specific point is, “Why add foam to the slurry?”
What the patent doesn’t get into at all is the reason that foam was added to the process of making gypsum board. The answer was to create a lighter piece of gypsum board. Long term bodily harm to drywall hangers was the driving force behind the invention of gypsum board that weighed less. In the old days, before the invention of lightweight drywall, sheets of gypsum board were heavy. As in very heavy. Over the years, those very heavy sheets took their toll on the backs, shoulders, elbows, etc. of people employed to install (in the trade drywall installers are called ‘hangers’), resulting in shortened careers and billions of dollars in medical costs.
There was a real need to find a way to make gypsum board lighter.
And that’s why foam was added to the manufacturing process.
This brings u right back to the 2013 patent discussed above. But why add silica gel to the manufacturing process? Answer: because foam was added. And…?
Well, let’s go back to the patent again:
[0005] In one aspect, the present invention provides a gypsum board comprising a set gypsum composition disposed between two cover sheets. The set gypsum composition comprises an interlocking matrix of set gypsum formed from a slurry comprising at least stucco, water, and metal silicate. The set gypsum composition comprises silica gel. The gypsum board has a density from about 15 lbs/ft to about 42 lbs/ft and a Fire Endurance Index greater than about 53 minutes.
[0006] In another aspect, the present invention provides a method of increasing fire endurance of a gypsum board comprising forming a slurry comprising stucco, water, and metal silicate, disposing the slurry between two cover sheets to form a board preform, cutting the board preform into a gypsum board of predetermined dimensions after the slurry has hardened sufficiently for cutting, and drying the gypsum board. At least a portion of the metal silicate converts to silica gel. The gypsum board has increased fire endurance as compared to a board having no silica gel
Quoted from U.S. patent #WO2015069609A1
The key phrase is, “the present invention provides a method of increasing fire endurance.” You see, by adding foam to the manufacturing process of gypsum board, companies were able to make it significantly lighter in weight. However, the tradeoff was that this lighter gypsum board was not as fire resistant as the heavier, denser gypsum board that had been manufactured without foam.
Thus the need to find a way to increase the fire resistance of the lightweight drywall.
Presto! Enter the 2013 patent.
The answer was to add silica to the manufacturing process of gypsum board. By doing so, the end product resulted in having a higher fire resistance than the same product without the silica added. And in order to meet national fire code regulations contained in the national building code, a way was found to make the lightweight gypsum board do just that. The full patent can be examined at this page.
Summary
So there you have it. Yes, gypsum board (drywall) contains silica. In decades past, the silica in drywall was there because in was simply abundant in nature and wasn’t filtered out from the gypsum used to make drywall. But since about 2013, silica is now added to the manufacturing process of making drywall (for reasons explained above), and modern gypsum board contains even more silica than its pre-lightweight predecessor.